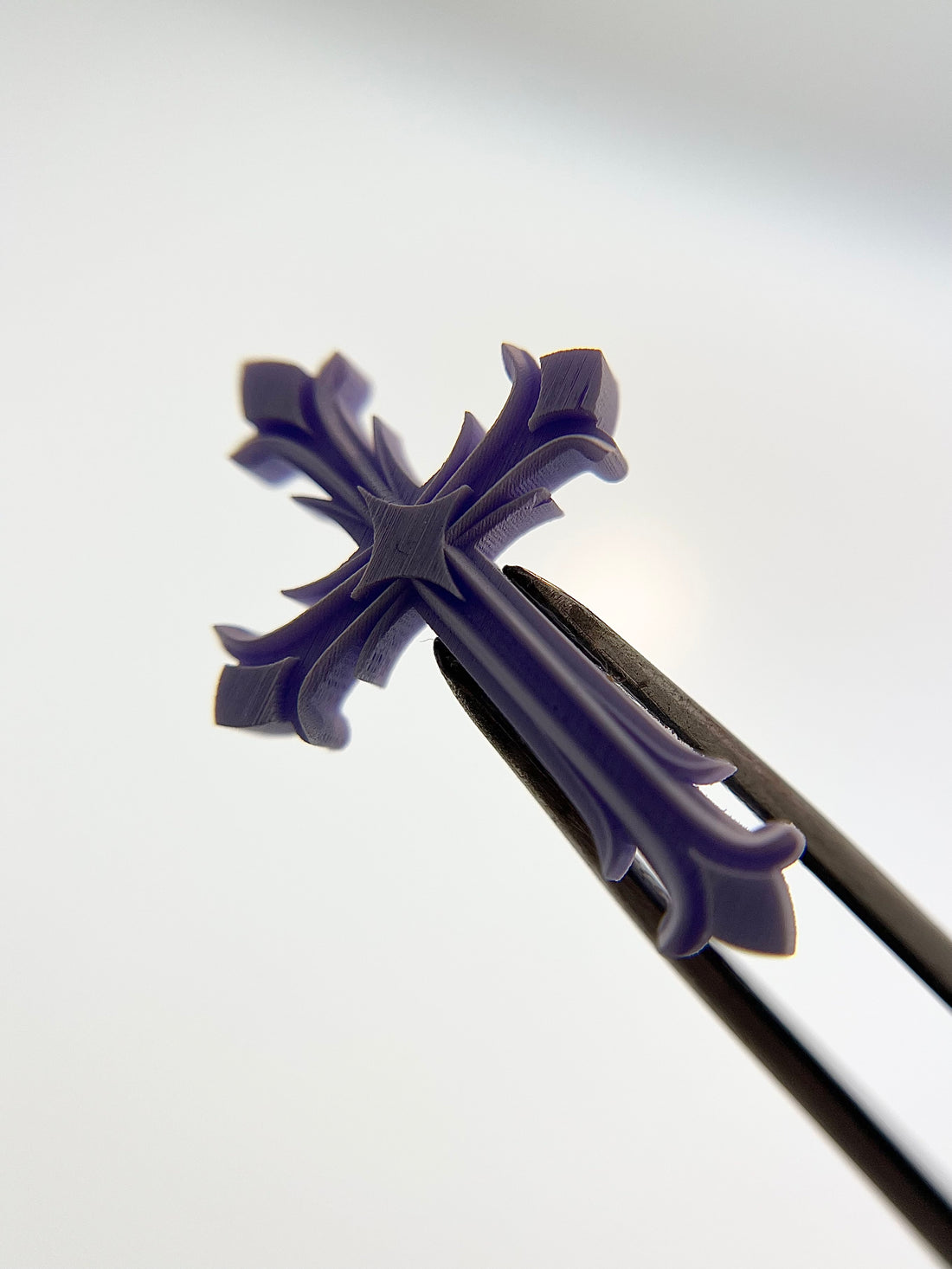
See How Your Jewelry is Made
Share
The Craftsmanship Behind The Masterpiece: A Closer Look
Creating custom jewelry is a blend of artistry, skill, and precision. From the moment a design is conceived to the final polishing, every step of the process is rooted in craftsmanship and a commitment to excellence. We specialize in transforming fine materials into stunning, one-of-a-kind pieces that tell your story.
Let’s take a closer look at the tools, techniques, and materials that bring custom jewelry to life.
The Finest Materials
Every custom piece begins with the best materials to ensure beauty and durability:
- Gold: Available in a range of colors—yellow, white, and rose—gold offers versatility and timeless elegance.
- Silver: Known for its brilliant luster, silver is perfect for creating modern, understated designs.
- Platinum: Durable and luxurious, platinum is ideal for intricate designs or pieces with larger gemstones.
- Gems: From diamonds and sapphires to emeralds and rubies, we work with both traditional and unique gemstones.
Sustainability: We also offer recycled metals and ethically sourced gemstones for clients looking to create responsibly.
The Crafting Process: From Concept to Masterpiece
Creating a piece of custom jewelry involves multiple intricate steps, each requiring precision and expertise:
1. Designing and 3D Printing
- Designs are first sketched and refined digitally.
- Advanced 3D printing technology brings the concept to life by creating a precise wax or resin model of the piece.
2. Casting
- Using the lost-wax casting method, the model is encased in a mold and heated to leave a cavity.
- The molten metal—gold, silver, or platinum—is poured into the mold, forming the base structure of the jewelry.
3. Cast Cleaning
- Once cooled, the cast piece is carefully removed from the mold.
- Excess material is trimmed, and the piece is cleaned to reveal its initial form.
4. Setting the Gems
- Stones are meticulously placed by hand using techniques like prong, bezel, or pavé settings.
- Each gem is secured to ensure both beauty and durability.
5. Enameling (if necessary)
- For designs that include vibrant, colorful accents, enamel is applied using traditional or modern techniques.
- The enamel is baked to achieve a smooth, durable finish.
6. Laser Engraving
- Precision laser engraving is used for intricate patterns, monograms, or personalized messages.
7. Polishing and Rhodium Plating
- Each piece is polished to perfection, removing any imperfections and achieving a mirror-like finish.
- White gold and certain silver pieces may be plated with rhodium to enhance their brilliance and protect against tarnishing.
The Time and Precision Required
Each piece of custom jewelry requires weeks—or even months—of careful work, depending on the complexity of the design. From the moment the wax model is created to the final polish, every detail is handled with care and expertise.
Why Custom Jewelry is Worth the Wait
Handmade jewelry crafted from fine materials and intricate techniques stands apart from mass-produced alternatives:
- Durability: Fine metals and secure gemstone settings ensure your piece lasts for generations.
- Uniqueness: Each piece is a one-of-a-kind reflection of your vision and style.
- Quality Craftsmanship: Every detail, from engraving to polishing, is done with precision, ensuring perfection.
Why Choose Us?
Our expertise spans every step of the process, from sourcing fine materials to executing the most intricate techniques. Whether you’re designing a new piece or repurposing sentimental heirlooms, we take pride in crafting jewelry that exceeds your expectations.